Delays and budget overruns are increasingly prevalent in the design industry. Extended design and bidding phases and inadequate collaboration between architects and construction teams often lead to increased costs and material waste. This can cause projects to fall behind schedule or exceed budget expectations, causing frustration for clients and stakeholders. The question is: how can the design industry optimize the project delivery process?
One viable approach is prefabrication. Prefabricated construction is known for speeding up timelines, minimizing risks, and elevating overall quality. However, a cultural shift is required to truly transform the industry. It is imperative to reassess traditional practices, adopt new methodologies, and encourage enhanced collaboration between designers and prefabrication manufacturers. By thoroughly examining both the benefits and constraints of prefabrication and consulting with field experts, the industry can fully harness its potential, achieving greater efficiency and cost-effectiveness in project delivery.
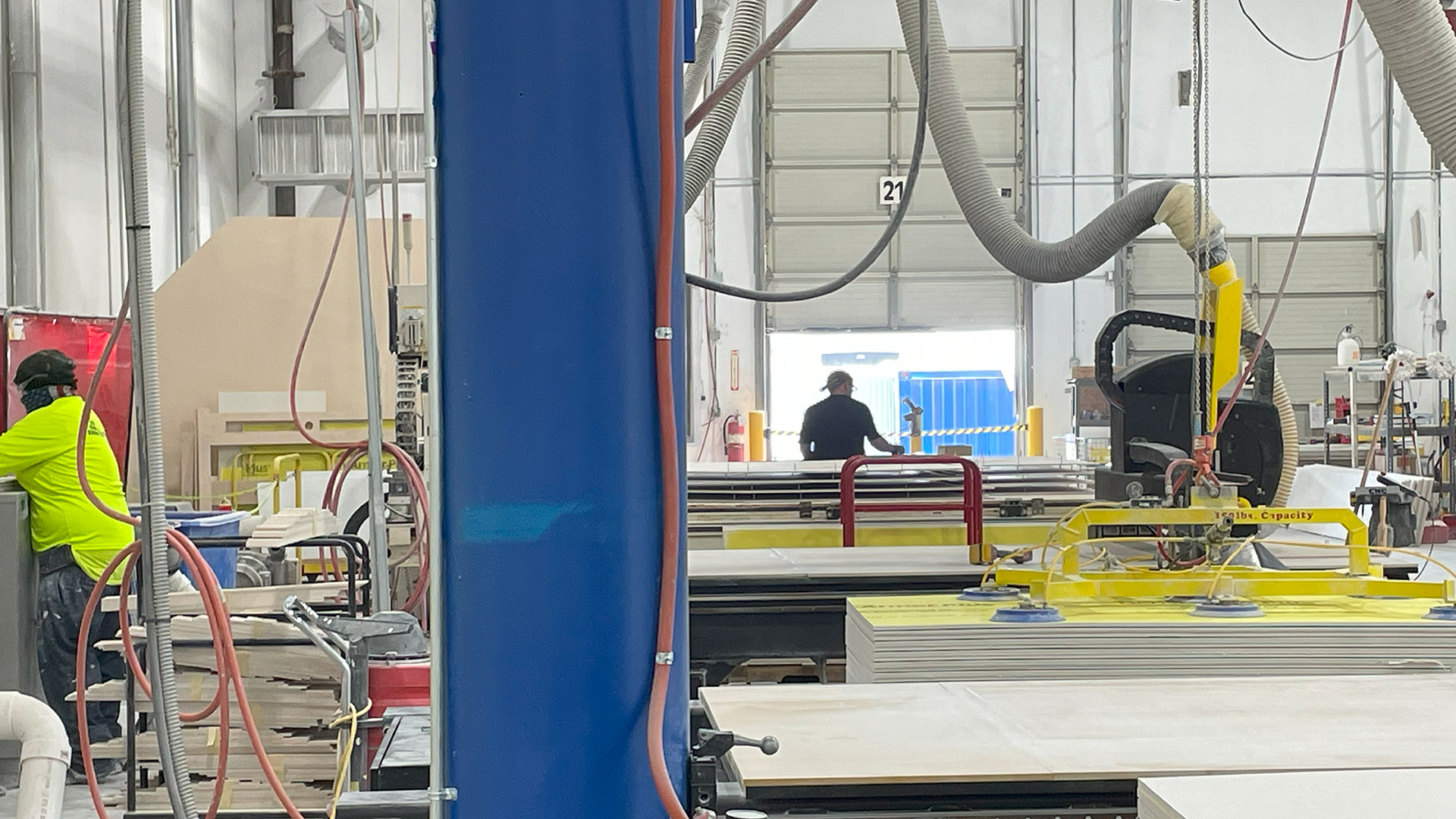
MAKING BIG IMPACTS WITH SMALL SCALE
In design, prefabrication is typically associated with projects involving significant repetition. But what if it also proves beneficial for intricate, non-repetitive structures?
People often equate prefabrication with modular construction, yet the two concepts are distinct. Modular construction is a subset of prefabrication, not synonymous with it.
- Prefabrication is a broad term encompassing any building system or components, such as walls, plumbing, flooring, and structural elements, manufactured offsite and assembled on the construction site.
- Modular Construction, on the other hand, refers specifically to prefabricated building units like complete rooms or sections of rooms. These units are produced offsite and transported as large “modules” to the construction site, where they are assembled to form the complete structure.
A more comprehensive view of prefabrication reveals its potential to extend beyond repetitive design, possibly transforming construction practices.
One significant benefit of prefabricated assemblies is their ability to integrate smoothly into the design process from the outset. Utilizing a shared Revit model allows both designers and builders to remain synchronized with the latest plans, which enhances accuracy and reduces the likelihood of mistakes. The adaptability of modular designs provides substantial flexibility, paving the way for greater innovation and efficiency.
In addition to delivering high-quality finishes, modular assemblies streamline labor, reduce punch lists, and support just-in-time (JIT) delivery. This accelerates construction timelines and can even fast-track Authority Having Jurisdiction (AHJ) approvals from third-party inspectors, who often review the assemblies directly at the prefab factory. The outcome is a more intelligent, expedited, and efficient method of construction.1
However, it’s important to note that prefabrication has its drawbacks. It isn’t suitable for every project. Economically, it can sometimes require a higher initial investment compared to traditional construction methods. Additionally, it demands meticulous planning and coordination, including a precise schedule to ensure all components arrive on-site in a timely manner. Aesthetically, there may be design limitations for custom pieces due to site conditions, transportation logistics, or the need for specialized machinery. Despite these challenges, prefabrication still offers a promising trend towards a more sustainable, efficient, and cost-effective design approach.
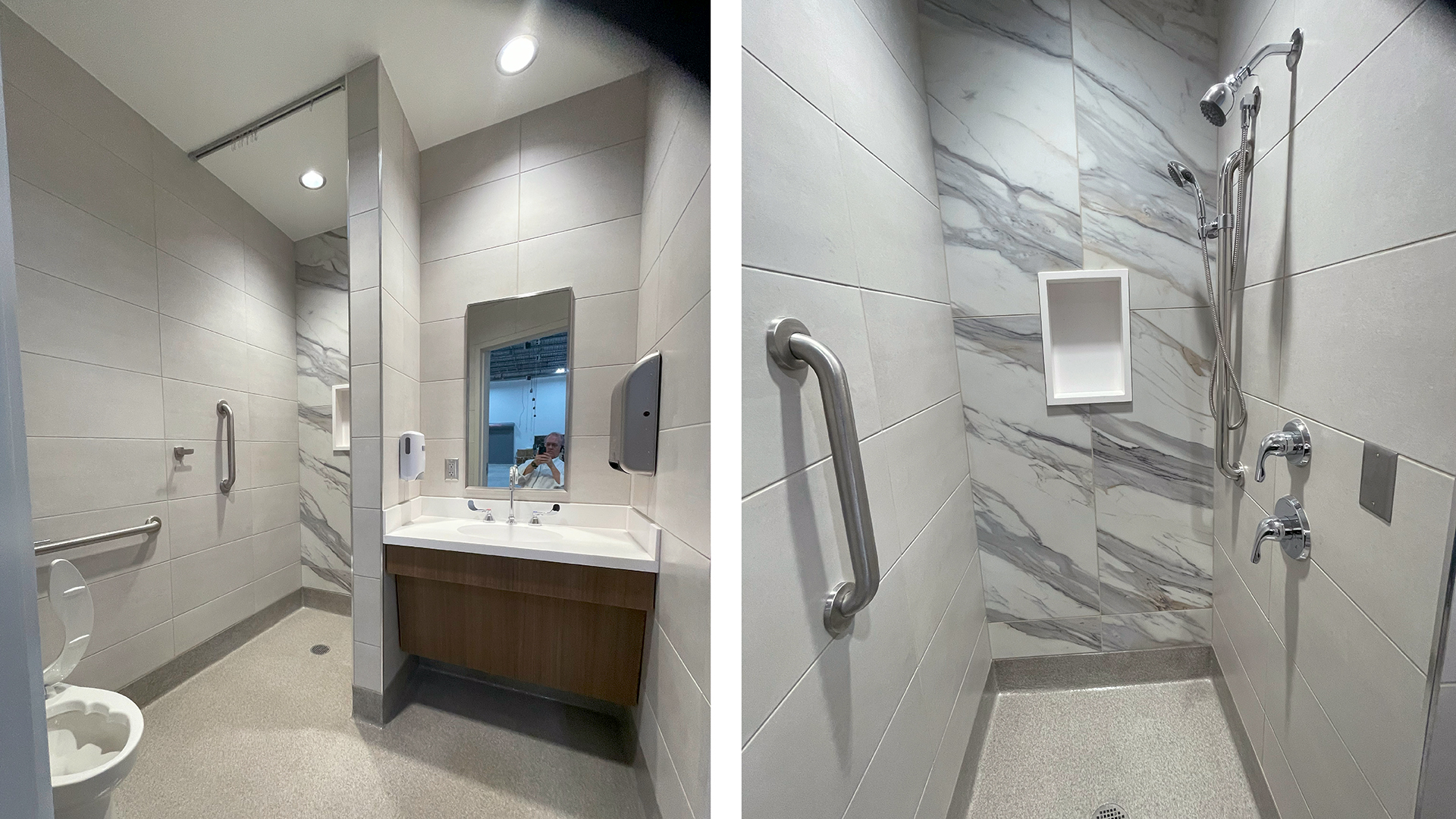
SurePods
Little’s healthcare team from our Orlando office recently toured the SurePods facility to gain valuable insights into the versatility of modular design and construction. SurePods specializes in prefabricating bathrooms and kitchen pods, a mass-production process that adds significant value for clients in healthcare, hospitality, multi-family housing, and beyond.
John Donohue, our host, gave the team a detailed overview of SurePods’s prefabrication services. The tour—which, for safety, was held after production hours—took us through conference, design, and training spaces before heading to the factory floor, where we observed the fabrication process in action at each station. The factory is fully equipped to handle every production stage, offering a firsthand look at how mass-producing these essential building components drives efficiency and quality across various projects.
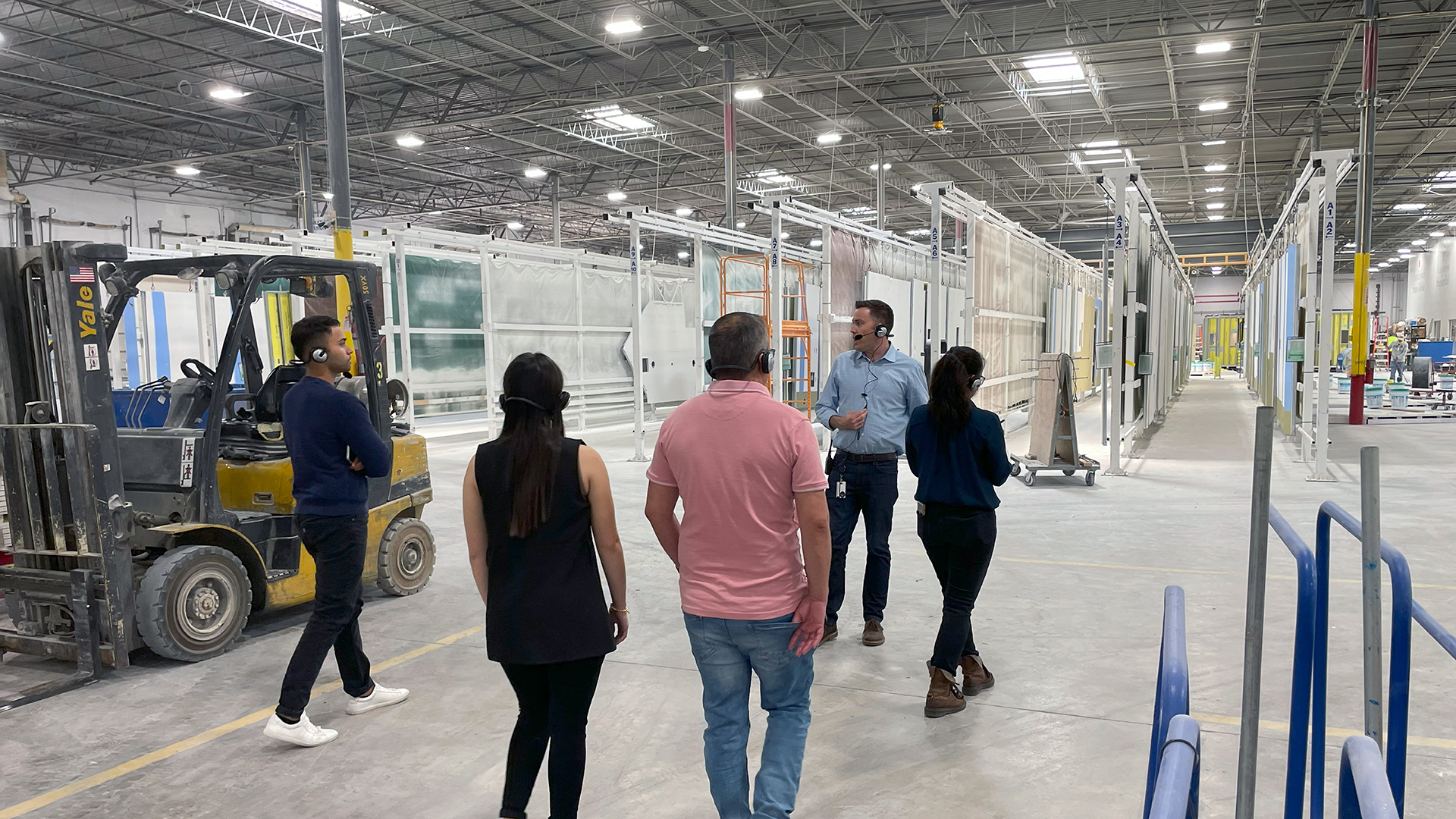
INTEGRATION OF THE PREFABRICATION INTO THE PROJECT TEAM’S DESIGN PROCESS
During the SurePods tour, we learned how many decisions go into designing each pod before the first basket of parts is pulled from inventory. SurePods provides a range of pre-construction services to help design teams navigate the possibilities and limitations of prefabrication.
These services include:
- Case studies, success stories, and lessons learned from past projects.
- Guidance on pod geometry and layout developed in collaboration with the design team.
- Advice on fixtures and finishes based on owner preferences.
The architect and engineer are instrumental in shaping and finalizing the design through an iterative process of ideas and feedback. Their contributions include:
- Steering owner decisions through each design stage and during mockup reviews.
- Evaluating design options, from large-scale modular considerations to detailed finishes.
- Documenting selections based on input from the owner and SurePods.
- Planning for slab recesses, structural support, and integration with the overall building design.
- Ensuring compliance with building codes and designing connections for utilities.
Owner input is key to achieving a successful product. Owners provide:
- A functional description of their needs.
- Preferred design options, fixtures, and finishes.
- Feedback on pod mockups.
Once assembled and shrink-wrapped, the pods are transported to the job site, ready to be inserted into the building shell after the structural frame, floors, roof, and corridor systems are in place. Delivered by rolling dollies, the pods are fitted into their pre-designated locations and connected to utilities for power, data, water, and drainage, seamlessly integrating into the overall structure.
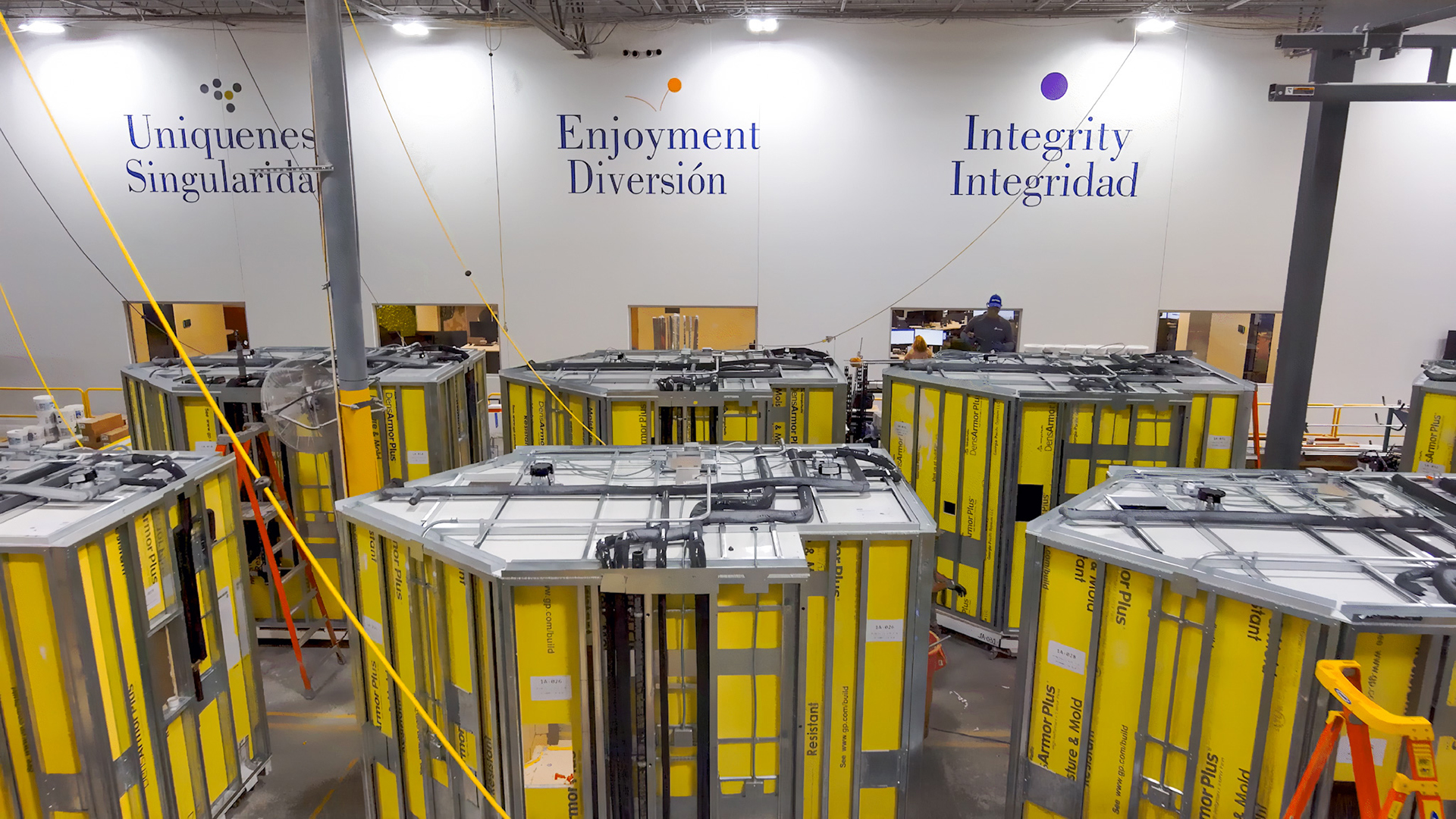
KEY TAKEAWAYS
As participants on the tour, we were intrigued by the integral role of prefabrication and its intricate construction process. The tour highlighted a more efficient and cost-effective approach for designers and clients, providing insights into the prefabrication of bathroom and kitchen modules from design to installation.
Several key themes stood out:
- The vital importance of coordination between the design team and the prefabricator.
- The success of the project hinges on careful planning from the earliest design phases, involving collaboration among the owner, architect, engineers, and prefabricator.
- A deeper appreciation for the flexibility that modular design and construction offer.
- An expanded view of the diverse applications for prefabricated assemblies.
- A clear understanding of the sustainable practices woven into each project, from material selection to assembly, delivery, and installation.
- The realization that prefabrication, even on a small scale, can have a significant impact on both project outcomes and efficiency.
Through this process, the potential of prefabrication to reshape construction became evident, offering not just innovation but a smarter, more sustainable way forward.
WHAT’S NEXT FOR PREFAB?
As construction evolves, prefabrication will play an increasingly powerful role, but architects must actively engage with this shift. Prefab isn’t just about breaking a design into parts; it requires collaboration with diverse systems and larger teams of stakeholders. Success hinges on precise timing, the use of new design tools, and adapting to constraints like equipment limitations, site conditions, and assembly needs specific to prefab methods. Suppliers may take on a larger role in project fulfillment, and documentation for regulatory approvals may require additional or different details.
While prefabrication offers numerous advantages, the design industry must adapt, continuously assessing when, how, and where to best implement these methods for maximum impact.
This article was co-authored by Mark Gilman, with contributions from Suraj Radadia.
RESOURCES
- “Standardizing Healthcare Facilities with Bathroom Pods.” SurePods. Accessed 23 May 2024. ↩︎